DETAILS INFORMATION
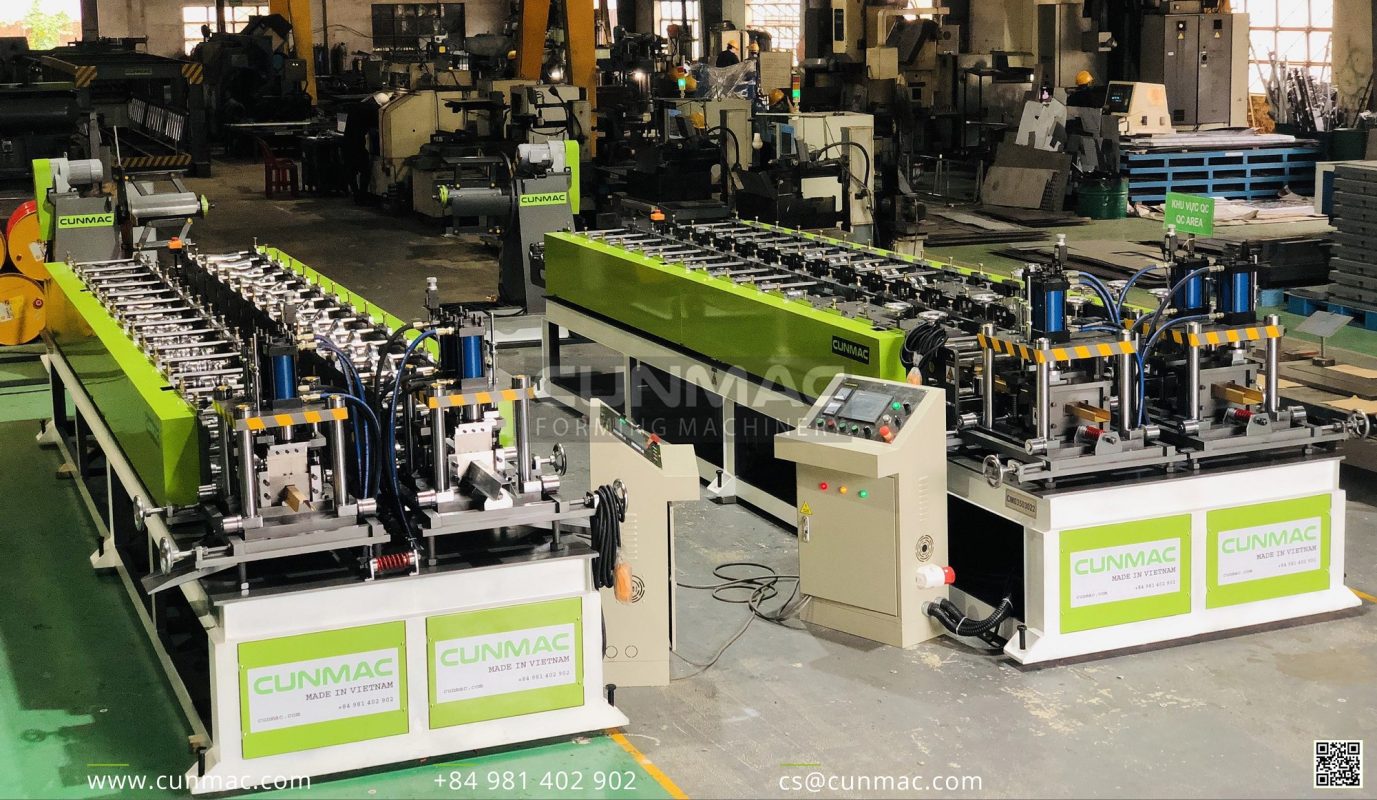
COMBINED ROLL FORMING MACHINE
The combined 2-in-1 roll forming machine is a machine that integrates two separate machines into one unit.
It is frequently used for producing lightweight channels, such as batten/top hat/hat channels, C trusses, C ceiling/furring channels, C studs, U tracks, V profile… with material thicknesses of less than 1.0 mm.
Some popular combinations: C stud & U track, C truss & Batten, Batten ceiling & Batten roofing, Batten & V profile…
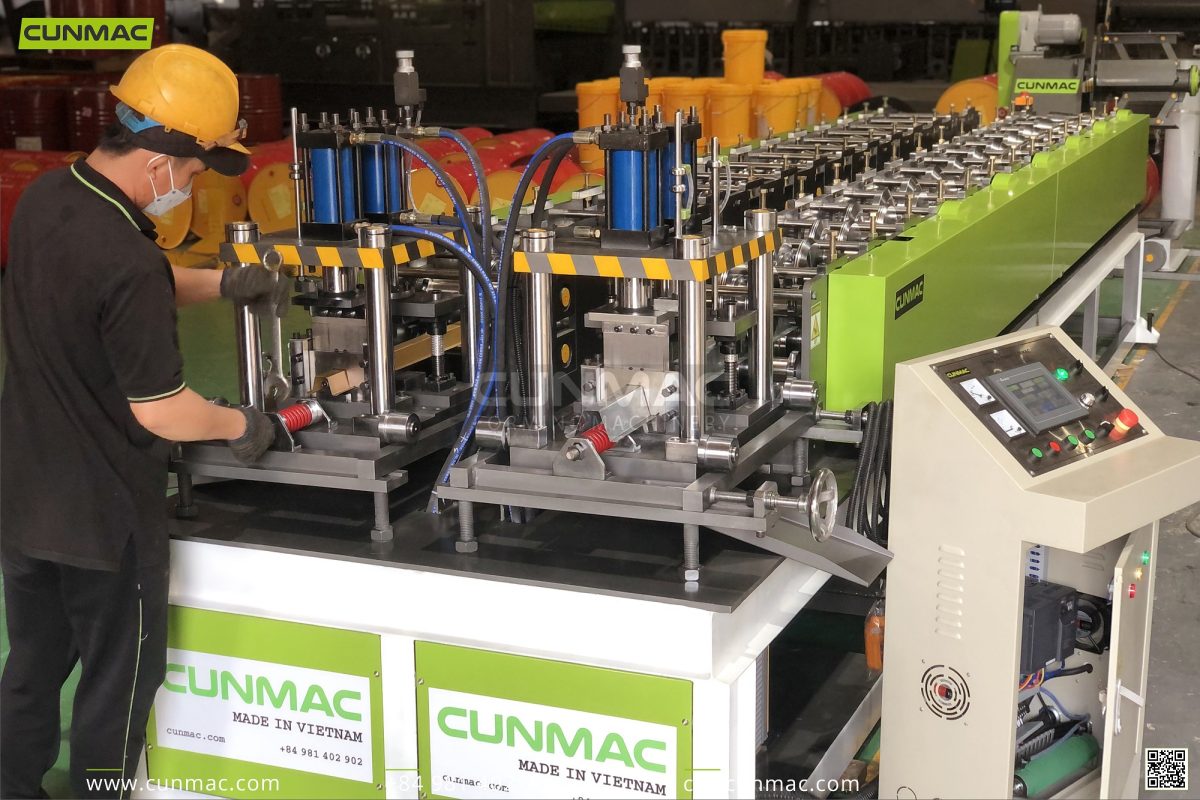
Combine batten & batten
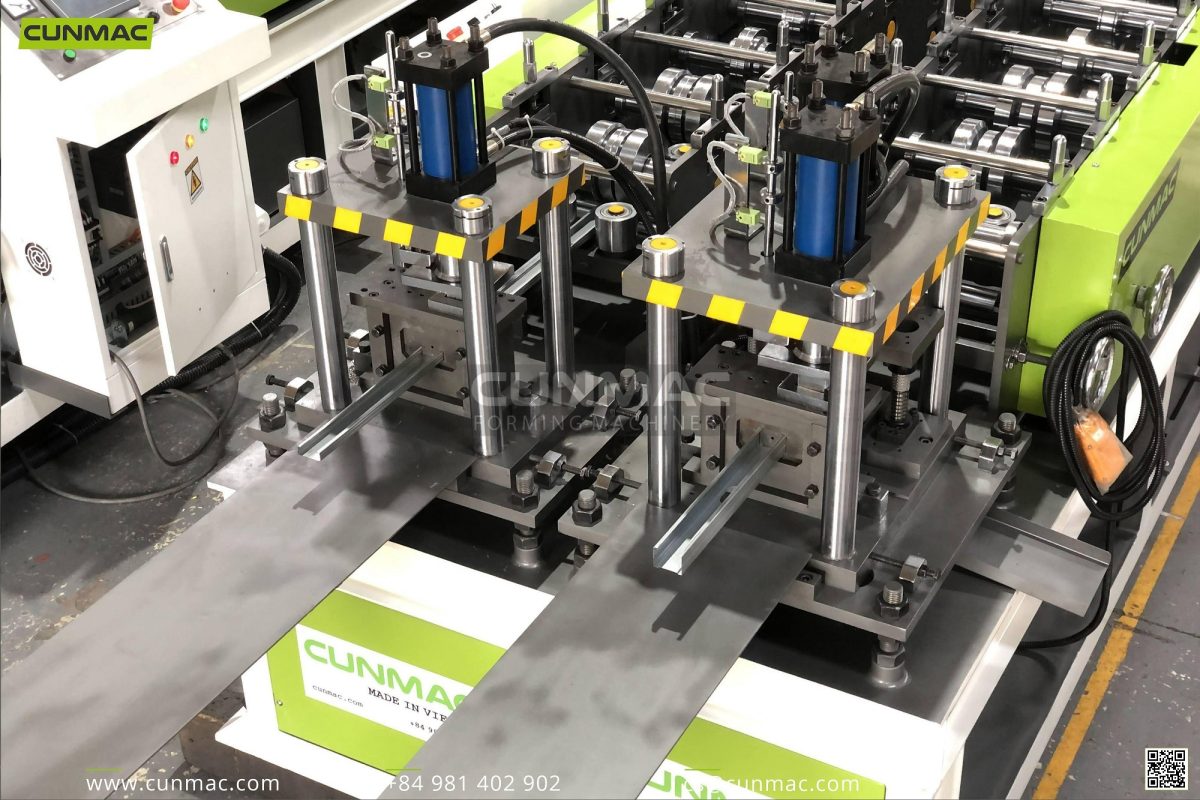
C truss & C truss
WHY COMBINED ROLL FORMING MACHINE?
1. Smoother operation for efficiency
This machine will maximize your production output by its continuous forming process and high-speed operation which can ensure faster and more efficient manufacturing, saving you valuable time and resources.
2. Higher durability and stronger frame
Electric roofing machine (non-hydraulic) is designed to have higher durability and a stronger frame compared to the hydraulic machine, to ensure a long lifespan and high production capacity.
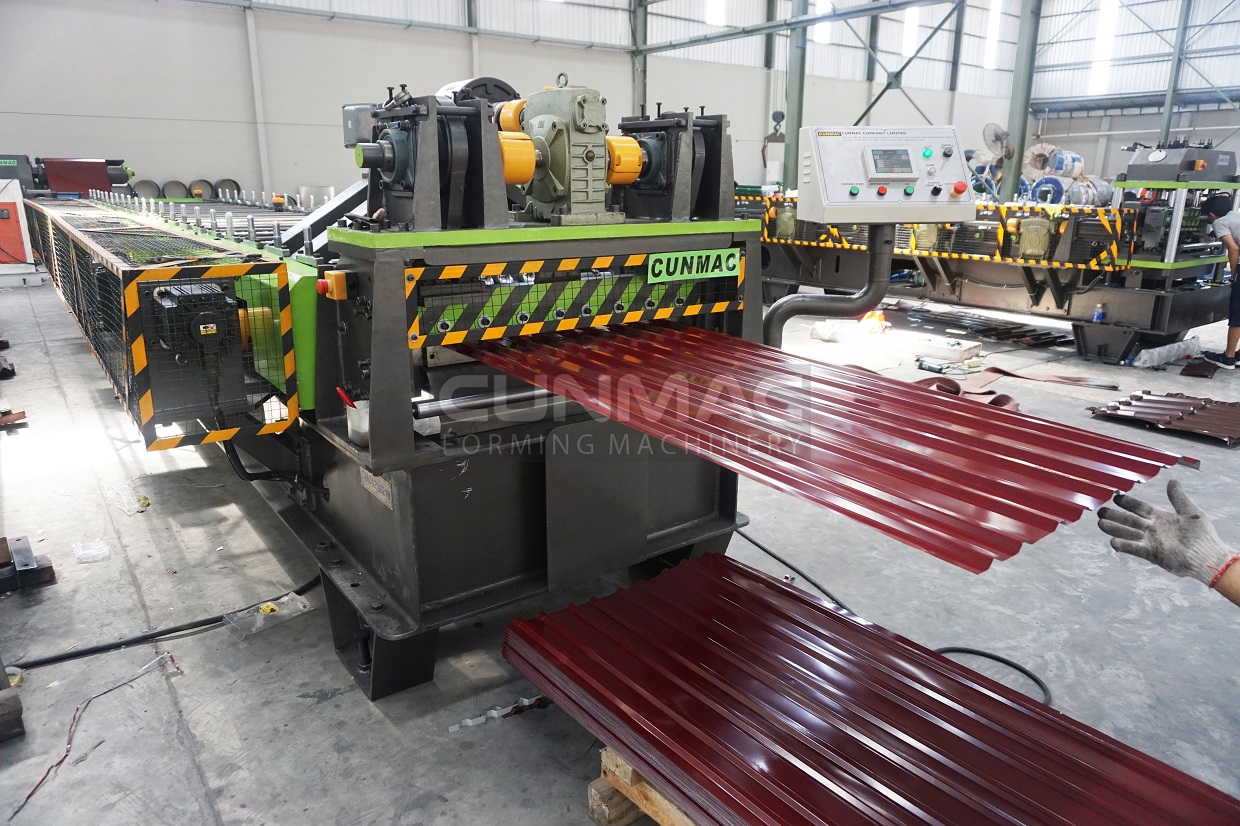
3. Cleaner factory without leaking oil
Electric roofing machines offer a cleaner factory environment without oil leaks, making them preferable, especially in high-temperature areas. They also reduce downtime and simplify maintenance procedures for roofing operators.
4. Eco-friendly and Sustainable
By utilizing 100% renewable energy, we ensure a sustainable future for generations to come. Join us in protecting the environment and empowering the next generation!
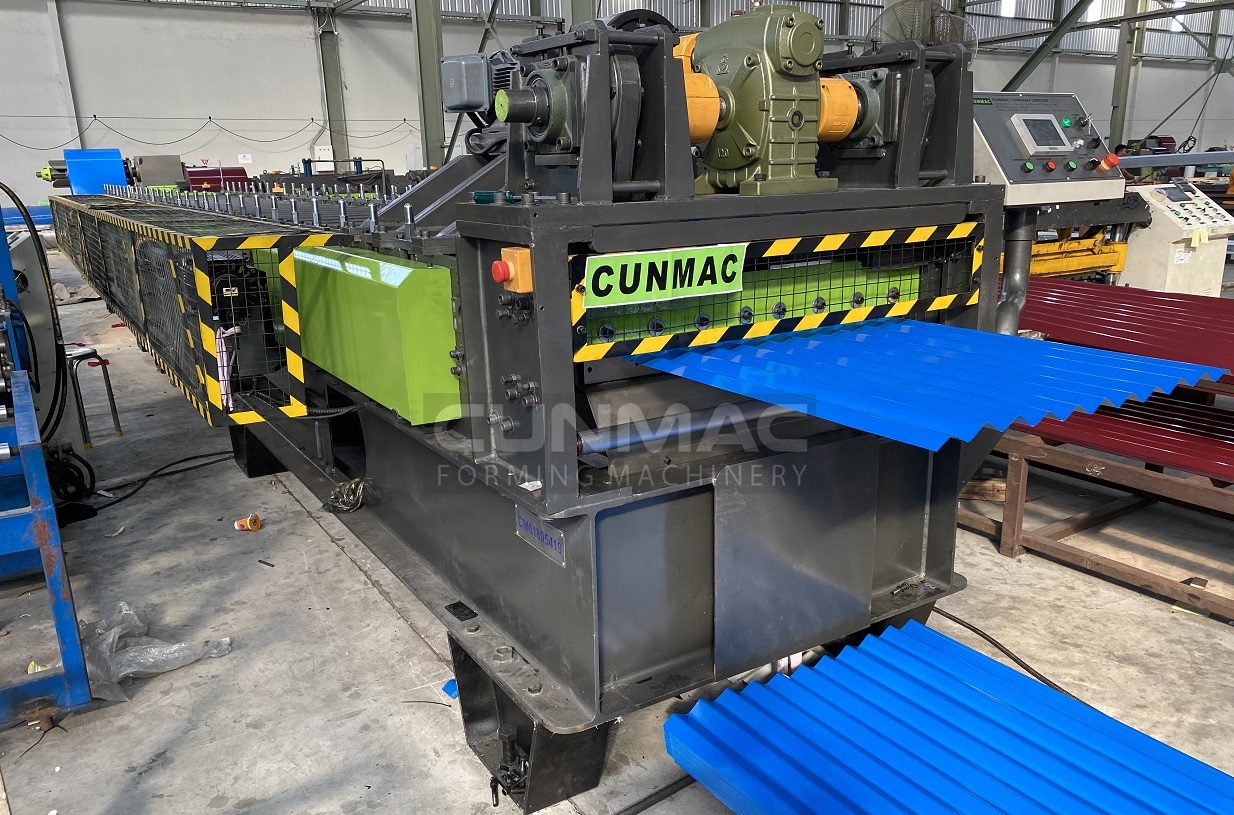
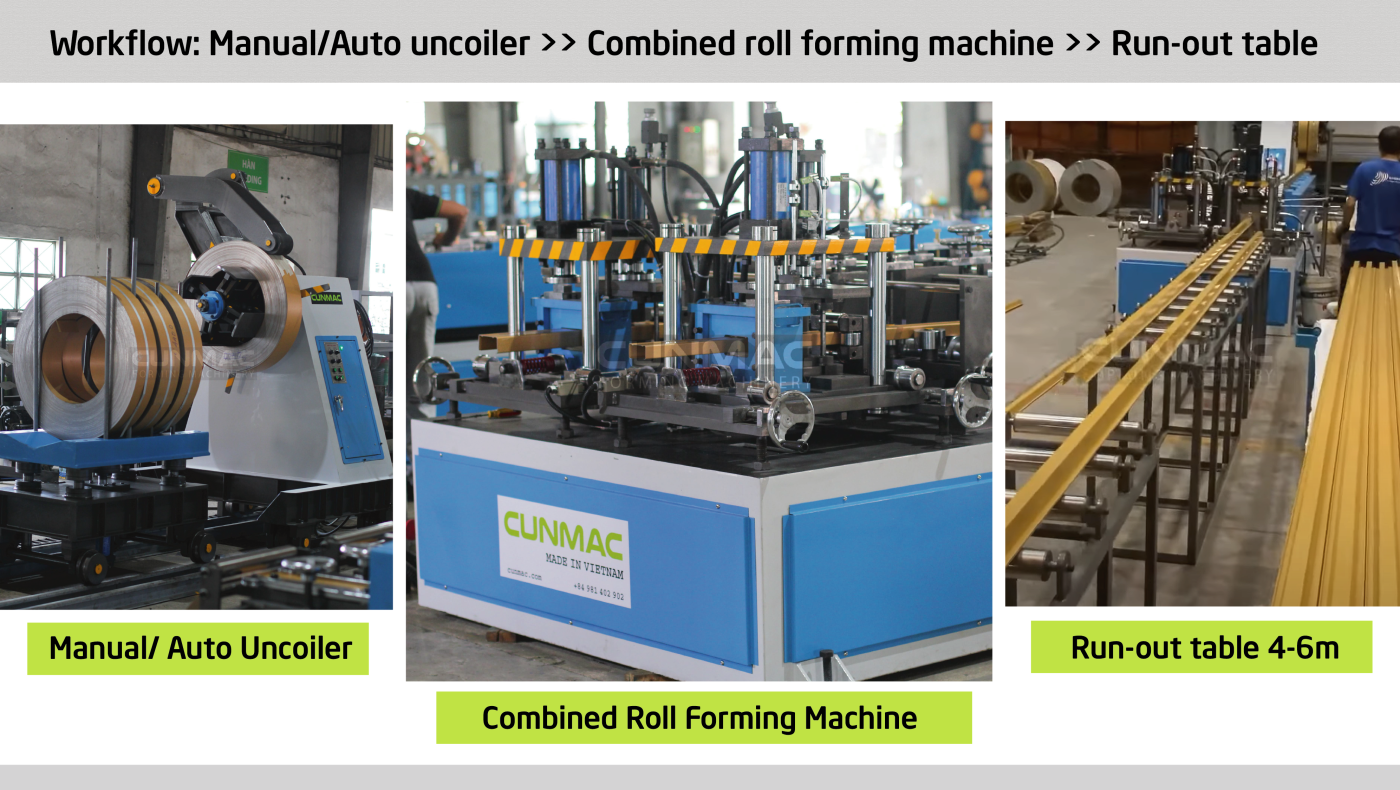
SPECIFICATIONS AND EQUIPMENT
- Automatic roll forming and cutting with Inverter, PLC, HMI
- Automatic programmable length settings via the touch panel
- Electrical and hydraulic components made from Japan, Germany
- Save history for orders in 30 days
- Customize design
- Stable operation with strong power and body frame
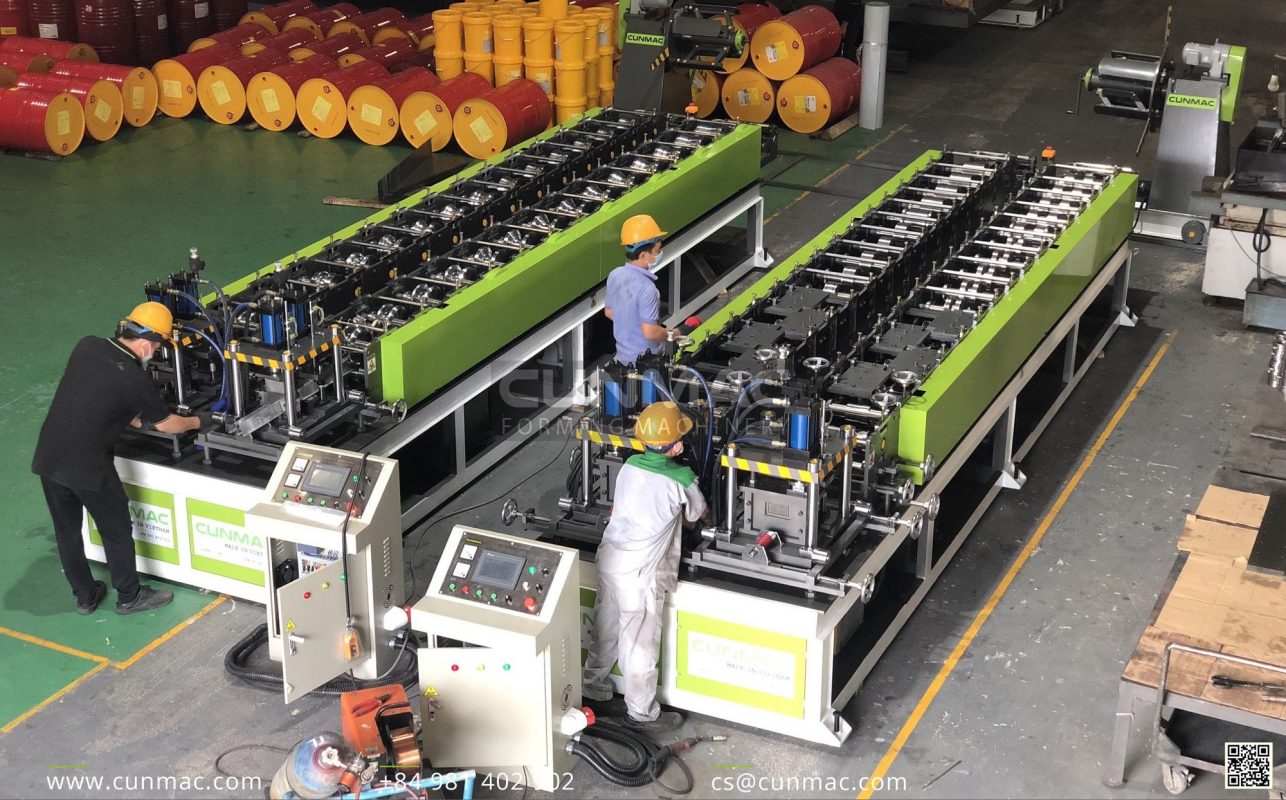
SPECIFICATION | |
Items | Details |
Total power | 5.5kw (3 phase, 50hz, 380v) |
Speed | 16 – 18m/min |
Dimension (LxWxH) | 5.0m x 1.2m x 1.6m |
Weight | 2.6 tons |
Roller station | 12 pairs |
Frame | I beam 200mm |
Material thickness | 0.4mm – 0.6mm |
Material width | 141mm |
Transmission system | Hydraulic |
Cutting system | Hydraulic cylinder (profile cutting system)
Material SKD11 Japan |
Control system | PLC, touchscreen |
Runout table | Manual 4m, 100kg load |
Manual uncoiler | 1.5 tons |
EQUIPMENT | |
Items | Brand |
PLC (CPU) | SIEMENS/MITSUBISHI |
Touch panel (HMI) | SCHNEIDER (France) |
Electric motor | HITACHI/TOSHIBA (Japan) |
Encoder, relay | OMRON (Japan) |
Inverter | MITSUBISHI (Japan) |
Hydraulic components | YUKEN (Japan) |
Cutting blades | SKD11 (Japan) |
Rollers | S45C, SKD11 (Japan) |
OPERATING COMBINED ROLL FORMING MACHINE AT CUSTOMER’S FACTORY
WHAT CUSTOMERS TALK ABOUT US?
Mr. Wong, Malaysia
“Hi team, so thank you for helping us with the installation. The production process is all good for now, V profile finish excellent 👍”
Mr. Denis, Angola
“Hey team! Our combine machine is our superhero during high-demand times! Thank you, keep up the fantastic work, everyone!”
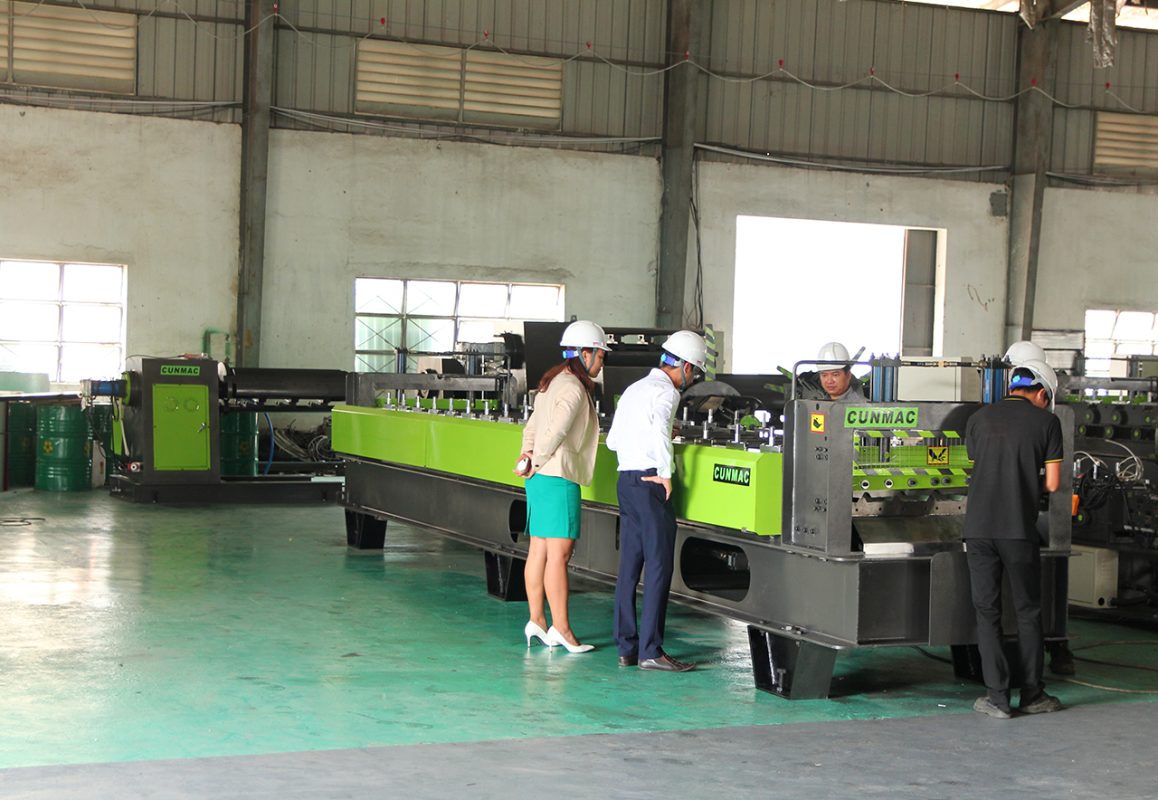
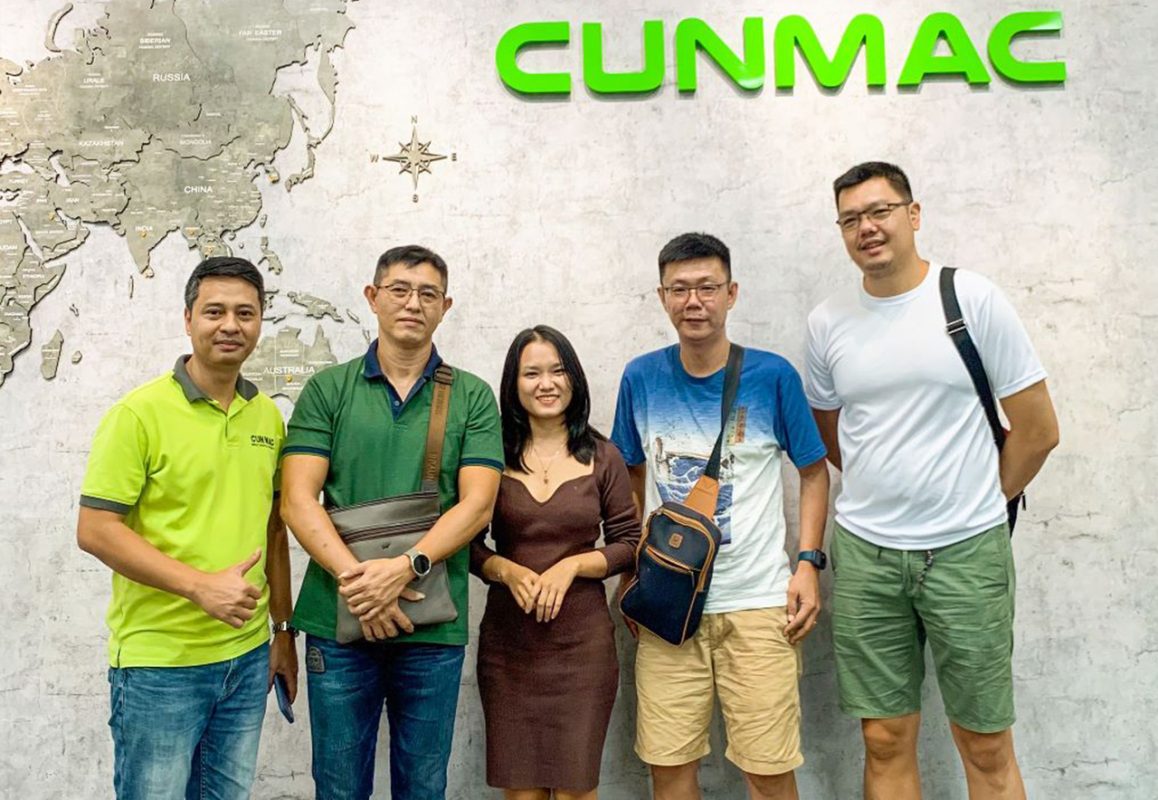
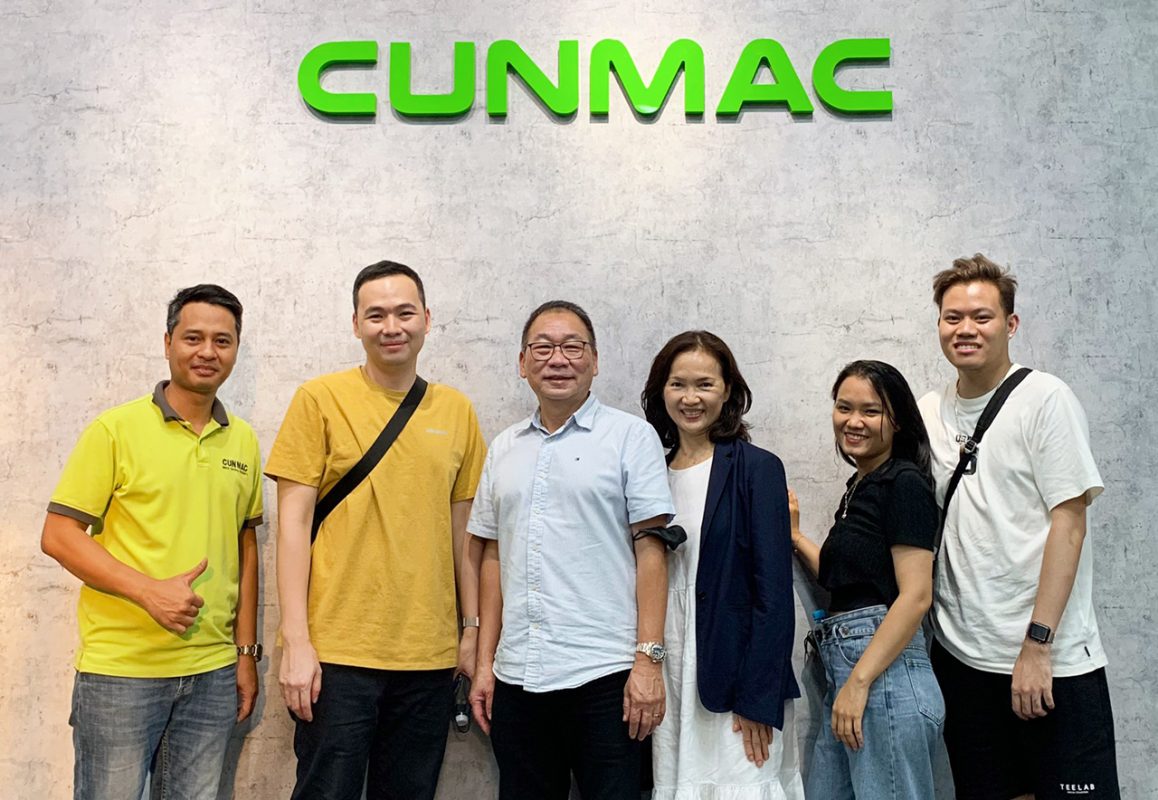
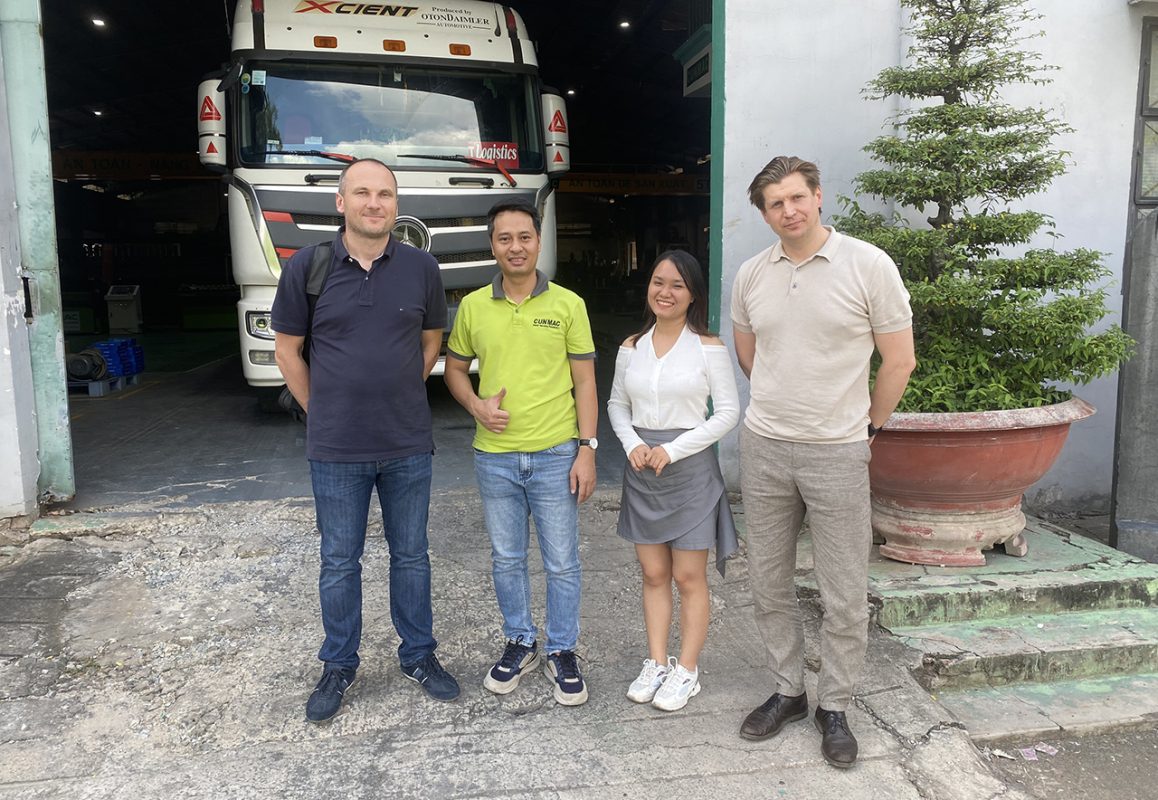
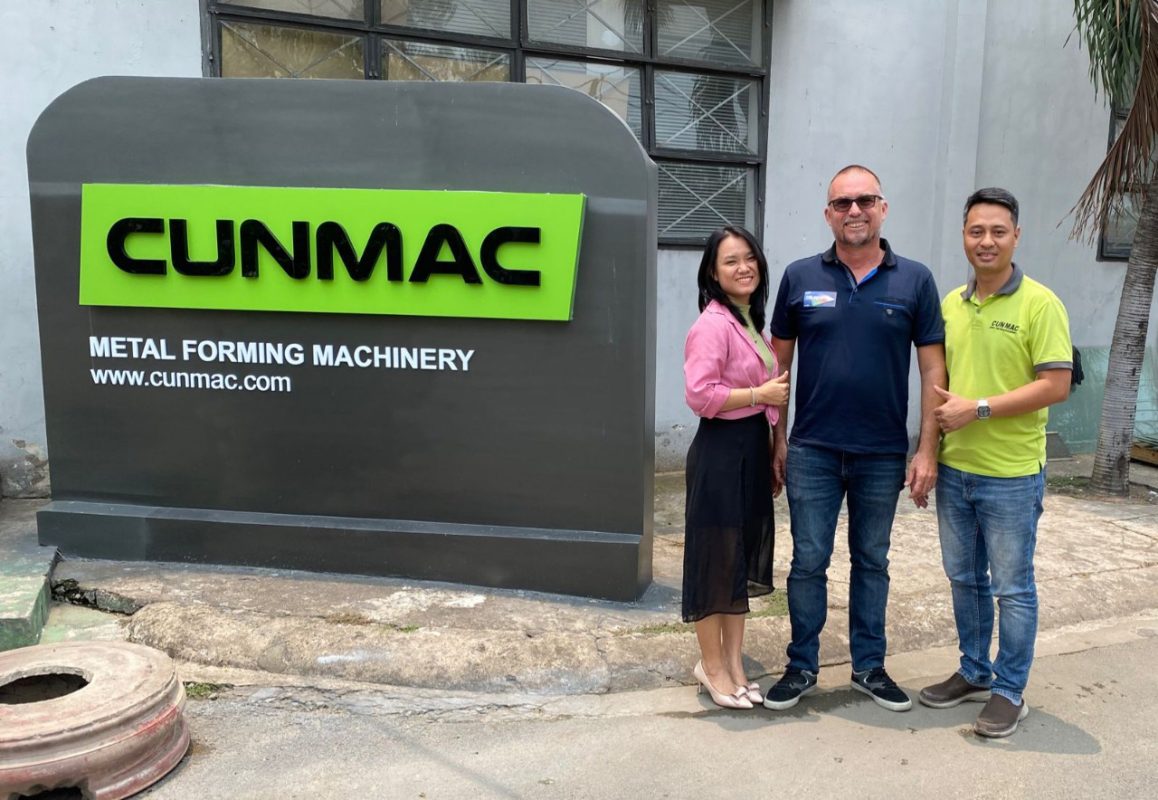
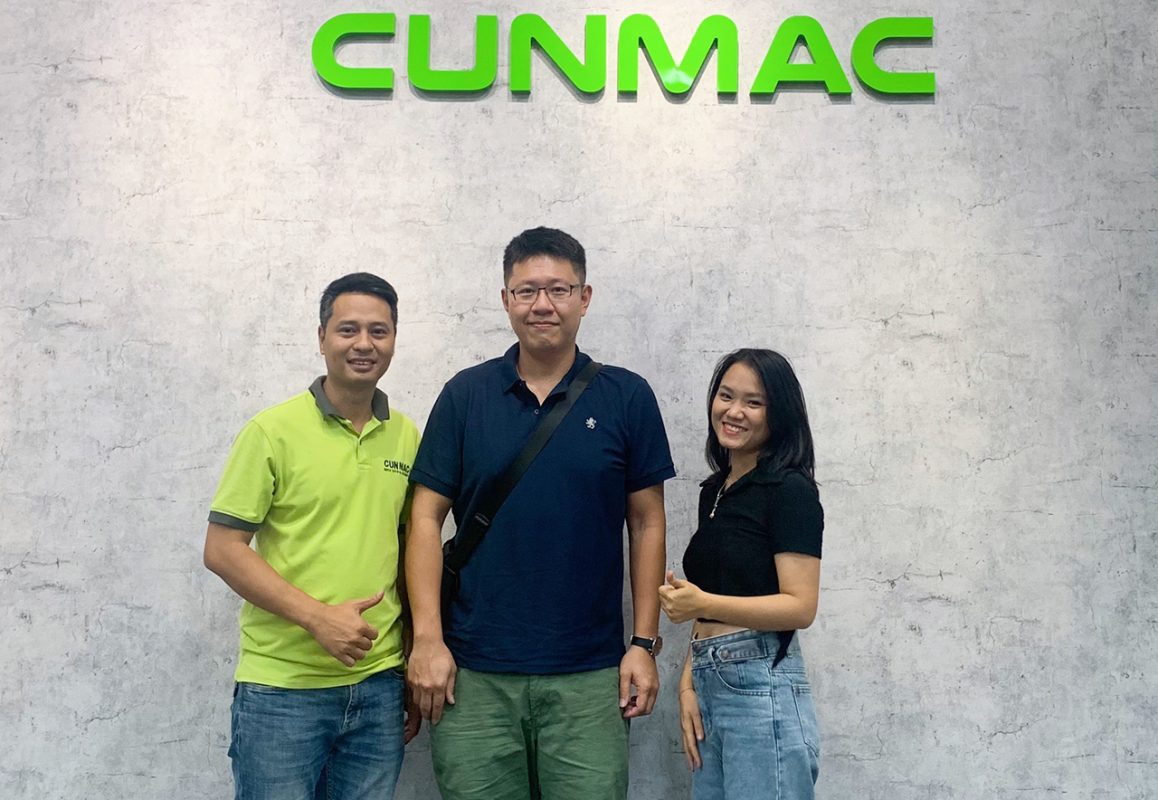
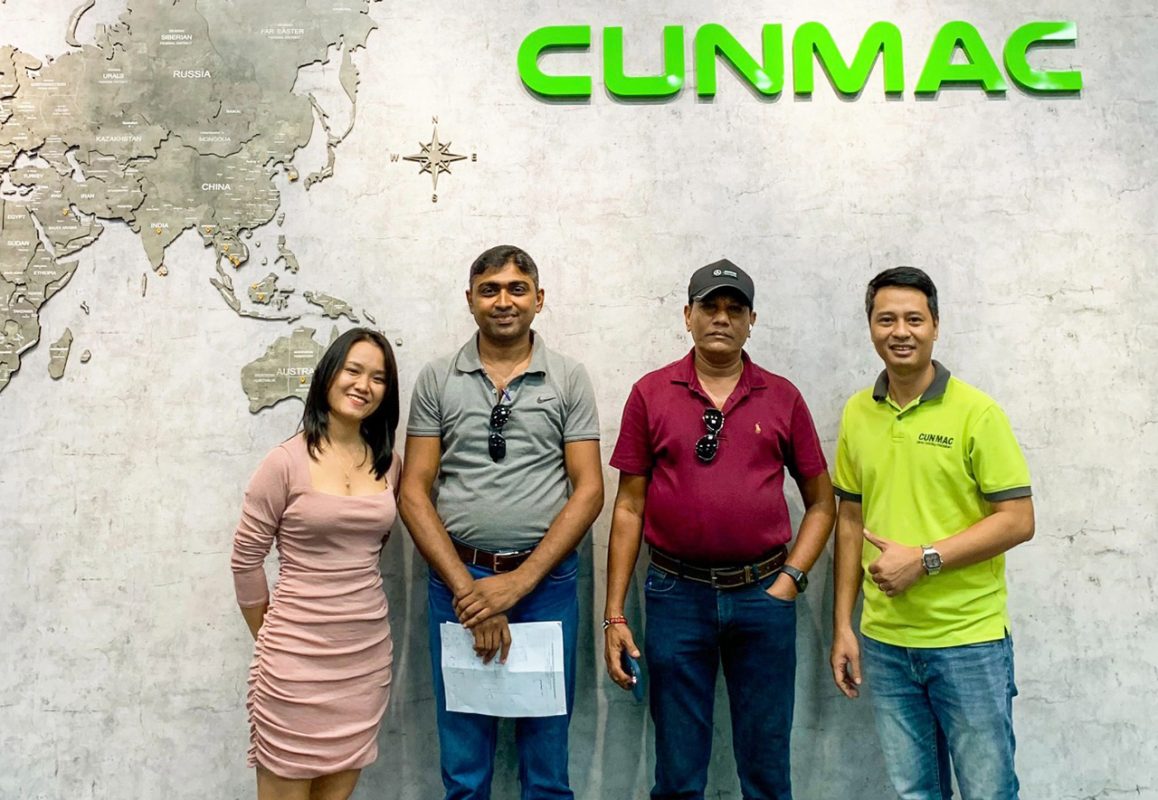
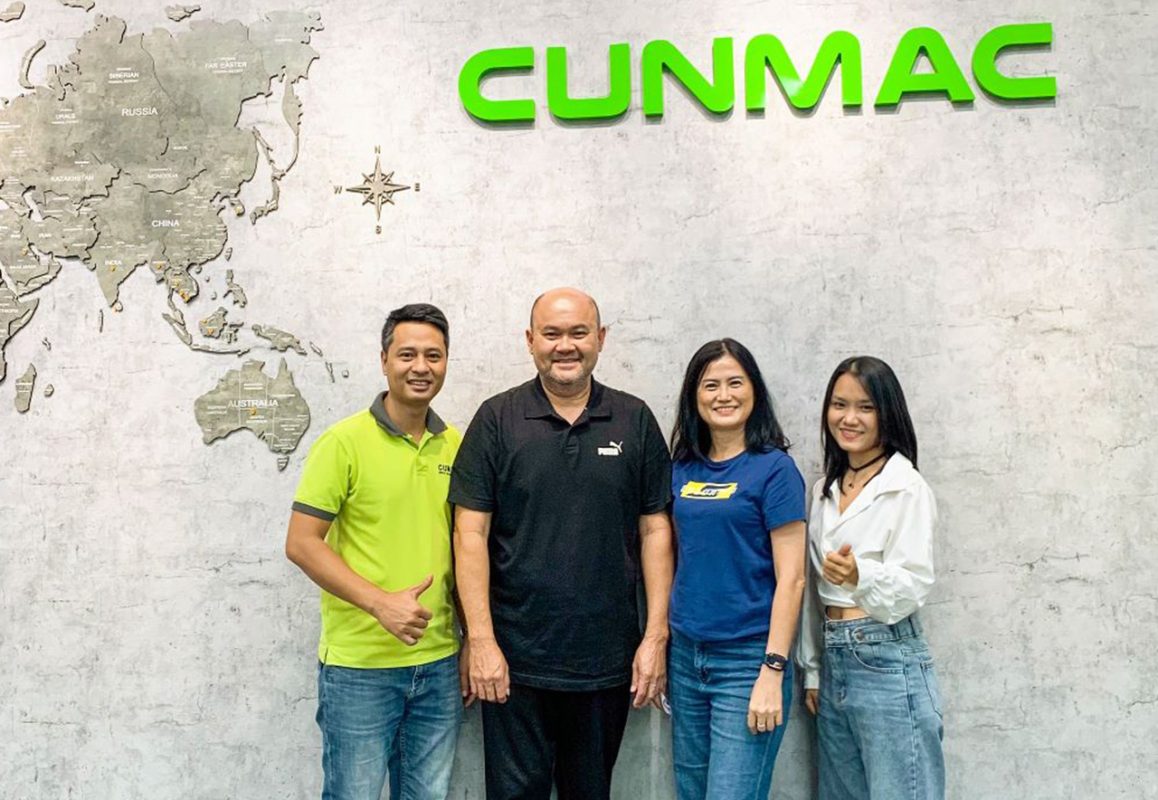
CUNMAC products reach 10% of their sales in the domestic market (Vietnam) and 90% are distributed across more than 30 countries over the world, including America, France, Korea, Australia, India, Angola, Ethiopia, Ivory Coast, Thailand, Myanmar, Indonesia, Malaysia, Sri Lanka, Kuwait, Cambodia, and Vietnam, among others.
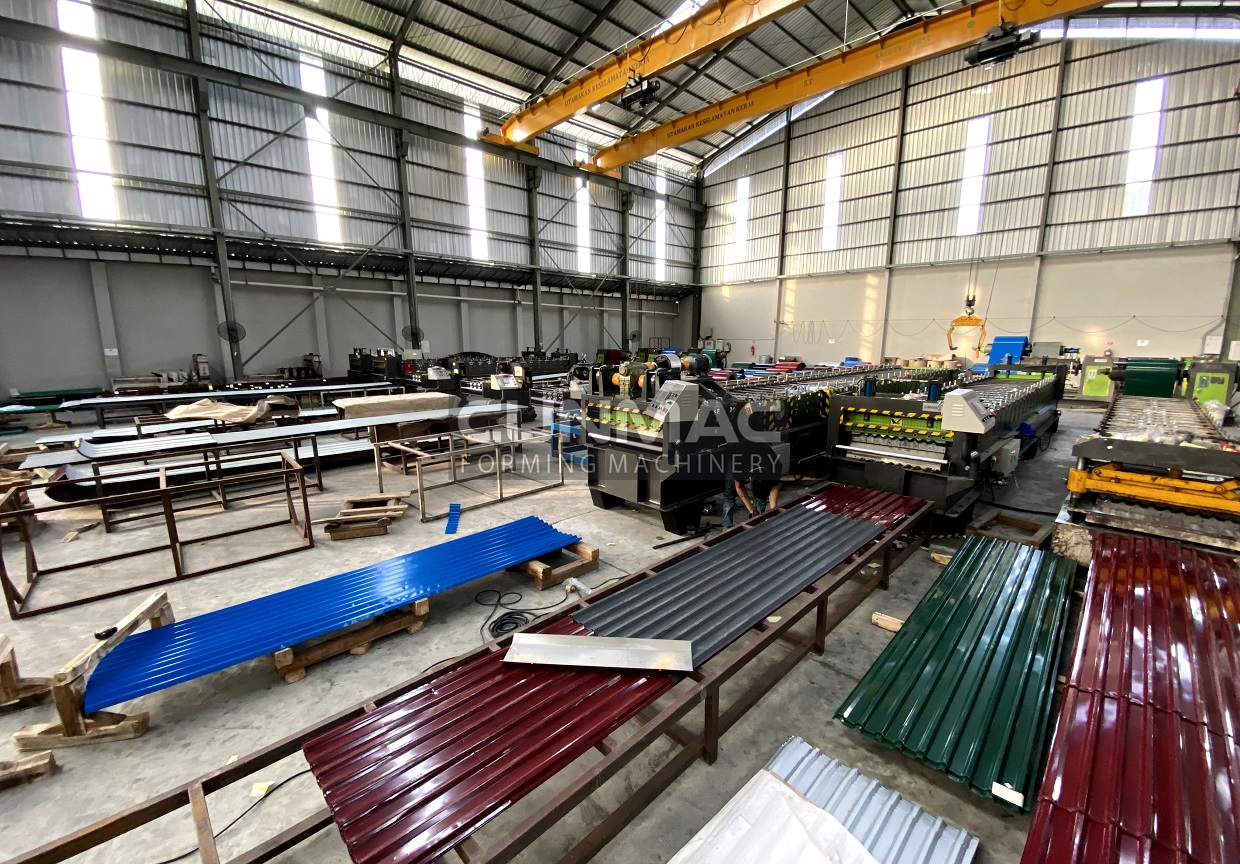
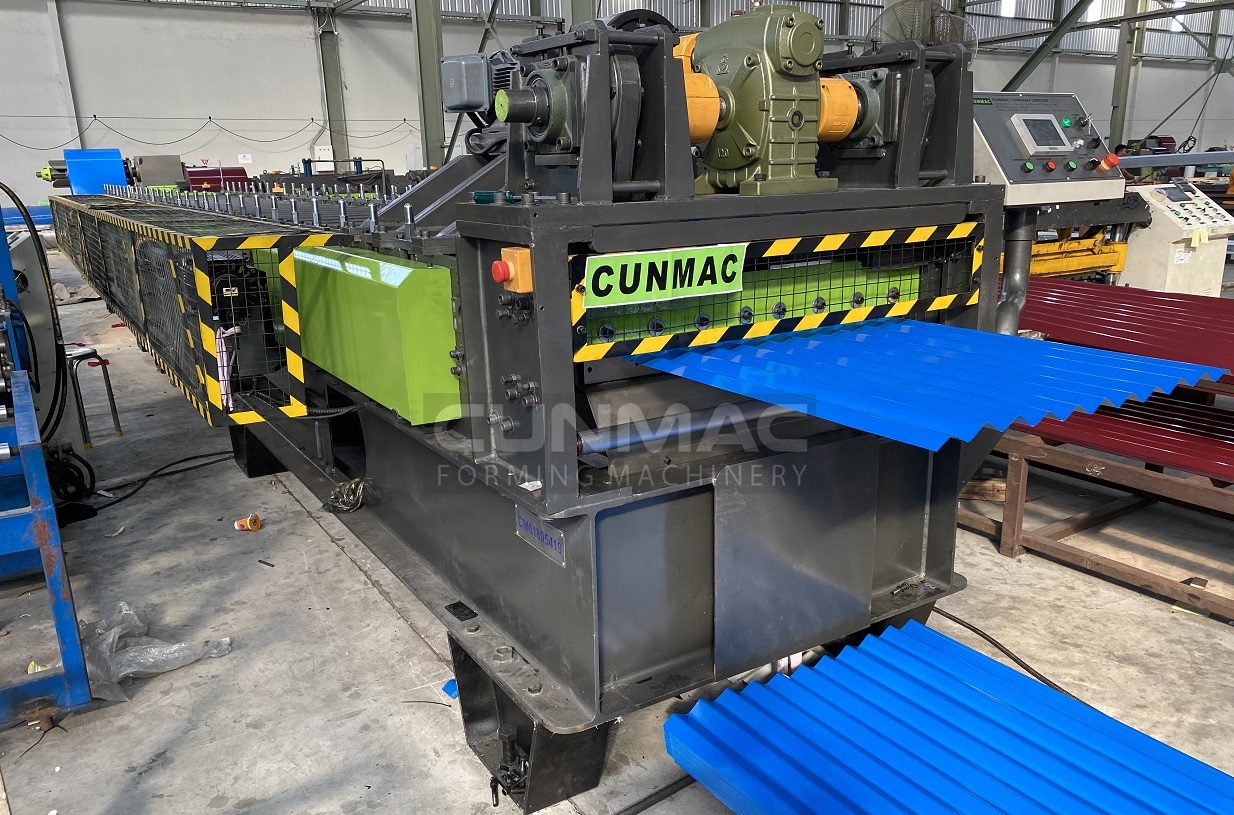
Are you ready to boost your factory’s performance?